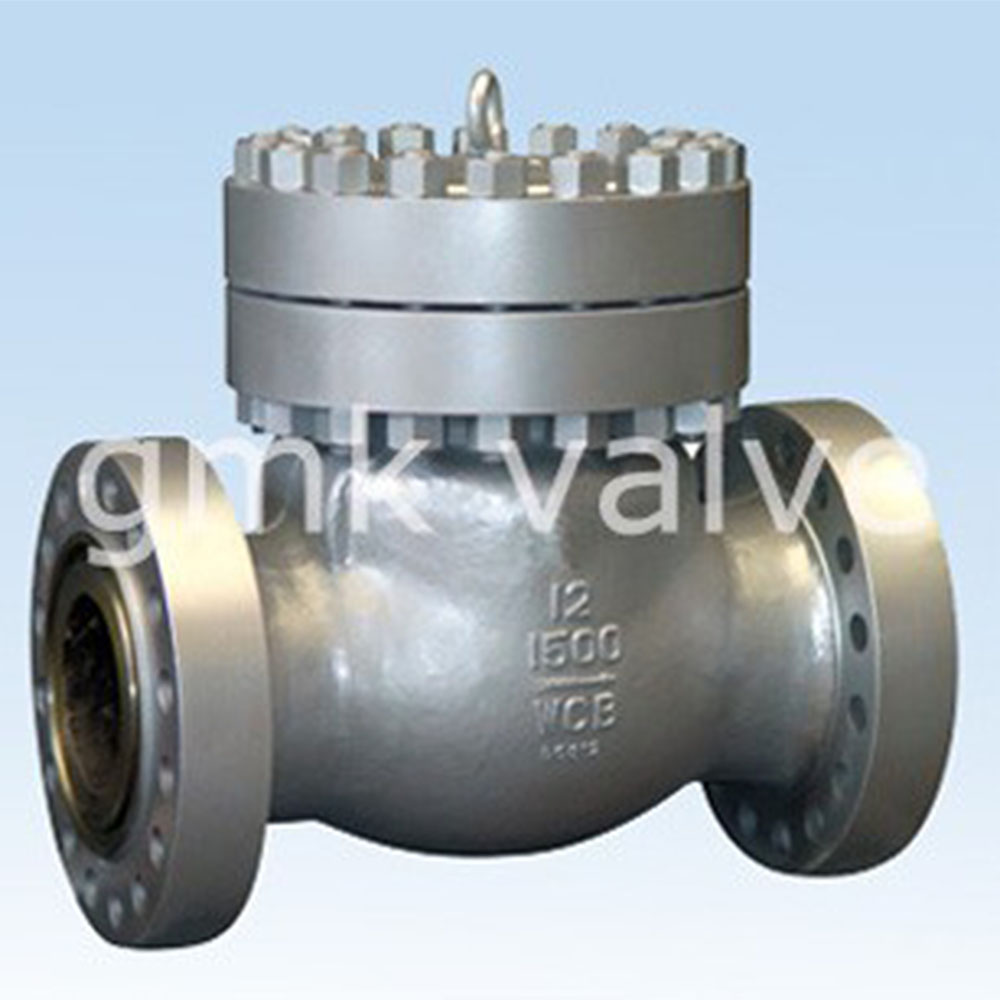
Have you ever wondered how the water in your home flows smoothly without any backflow? Or how fuel doesn’t flow backward when you turn off your car’s engine? The answer lies in a small but mighty device known as a check valve. This unassuming valve has been around for centuries and has played an essential role in regulating fluid flow across various industries. In this blog post, we will take a deep dive into the impressive history of check valves and explore their different types, workings, and importance. So buckle up and let’s embark on this fascinating journey through time!
What is a Check Valve?
A check valve is a type of mechanical valve that allows fluid or gas to flow in only one direction. It has an inlet and an outlet, and it prevents backflow by automatically closing when the flow reverses.
This simple yet effective device is commonly used in plumbing systems, water treatment plants, manufacturing facilities, automobiles, aircraft engines, and many other applications where fluid control is critical.
Check valves come in different shapes and sizes depending on their intended use. Some are designed to withstand high-pressure environments such as oil pipelines or chemical processing plants while others are made for low-pressure applications like household plumbing systems.
There are several types of check valves available including swing-check valves, ball-check valves, tilting-disc check valves among others that differ based on their design characteristics.
Check valves play a vital role in regulating fluid flow across various industries by preventing backflow which can cause damage or system failure if left unchecked.
The Different Types of Check Valves
Check valves come in different types depending on their design and application. The most common type of check valve is the swing check valve, which uses a hinged disc to regulate fluid flow. Another type is the ball check valve, which features a spherical sealing element that moves up and down to control the flow of liquid or gas.
Another popular design is the diaphragm check valve, which utilizes a flexible membrane to prevent backflow. This type of valve is commonly used in high-purity applications such as pharmaceuticals and food processing where there can be no contamination from outside sources.
In addition, there are also lift-check valves that contain a piston-like disk that opens when fluid flows through it but closes tightly against its seat when no water passes through it. There are stop-check valves that can perform both functions: they can act as an ordinary globe or gate valve while also providing automatic protection against reverse flow.
When choosing a check valve for your application, consider factors such as pressure rating, temperature range, materials compatibility with fluids being transported and maintenance requirements. With so many options available for various industries’ needs – from wastewater treatment plants to industrial manufacturing factories- selecting the right one will ensure efficient operation while minimizing downtime due to clogging or other issues caused by improper use of equipment.
How Check Valves Work
Check valves work by allowing fluid or gas to flow in one direction while preventing it from flowing in the opposite direction. They are designed to automatically close and prevent backflow, which can cause damage or contamination.
Check valves come in various designs, but they all have a similar mechanism of operation. The valve has an internal disc that moves freely within the valve body. When the fluid or gas is flowing in the correct direction, the disc moves out of the way and allows passage through the valve.
However, if there is any reverse flow, pressure builds up against the disc causing it to move into position and block off the opening. This reaction happens quickly and automatically without any external assistance needed.
The different types of check valves include ball check valves, diaphragm check valves, swing check valves and lift-check valves among others. Each type operates differently depending on its design.
In summary, Check Valves work by utilizing their internal mechanisms to allow forward flow while blocking reverse flow thereby protecting downstream systems from contaminants and damage due to backflow pressures.
The History of Check Valves
The history of check valves dates back to ancient times where simple forms of this valve were used in water systems. The Greeks and Romans also used similar valves for their aqueducts, although they were not known as check valves at the time.
The first documented use of a check valve was during the industrial revolution when steam engines became widespread. These early check valves helped regulate the flow of steam through pipes, which allowed machines to operate more efficiently.
During World War II, advancements in metallurgy and manufacturing led to new types of check valves that could withstand high-pressure applications. This allowed them to be used in military aircraft and submarines.
Today, modern technology has enabled the development of even more advanced types of check valves that are designed for specific industries such as oil and gas, chemical processing, and pharmaceuticals.
The history of check valves is a testament to human ingenuity and our ability to adapt technology over time. As industry needs to continue to evolve, so too will this vital piece of equipment that helps keep our machinery running smoothly.
Why Check Valves Are Important
Check valves are an essential component of many industrial and commercial processes. They play a vital role in preventing the backflow of fluids, which can cause serious problems such as contamination, damage to equipment, and even safety hazards.
One of the main reasons why check valves are important is their ability to prevent reverse flow. This means that fluids can only move in one direction through a pipeline or other system, ensuring that they reach their intended destination without interruption.
Check valves also help maintain pressure within a system by preventing fluid from flowing back into it. This helps ensure consistent performance and efficiency over time.
Additionally, check valves can help reduce maintenance costs by minimizing wear and tear on equipment caused by backflow or surges in pressure. By preventing these issues from occurring in the first place, companies can save money on repairs and replacement parts over the long term.
There are many reasons why check valves are important for businesses across a wide range of industries. From maintaining safety to improving efficiency and reducing costs, they play an essential role in keeping operations running smoothly day after day.
Conclusion
To sum it up, check valves are not just simple mechanical devices that allow fluids to flow in one direction. They have a rich history and play an important role in the functioning of various industries today.
From their earliest forms as flaps made from leather or animal skin, to the sophisticated designs of modern times, check valves have come a long way. Their evolution is a testament to human ingenuity and our constant quest for better solutions.
Check valves may be small but they serve a big purpose. They help prevent backflow and protect equipment from damage caused by reverse fluid flow. Without them, many industrial processes would not be possible or safe.
As we move forward into the future with even more advanced technologies, we can only expect that check valves will continue to improve and evolve alongside them. So next time you see a check valve at work, take a moment to appreciate its impressive history and significance!